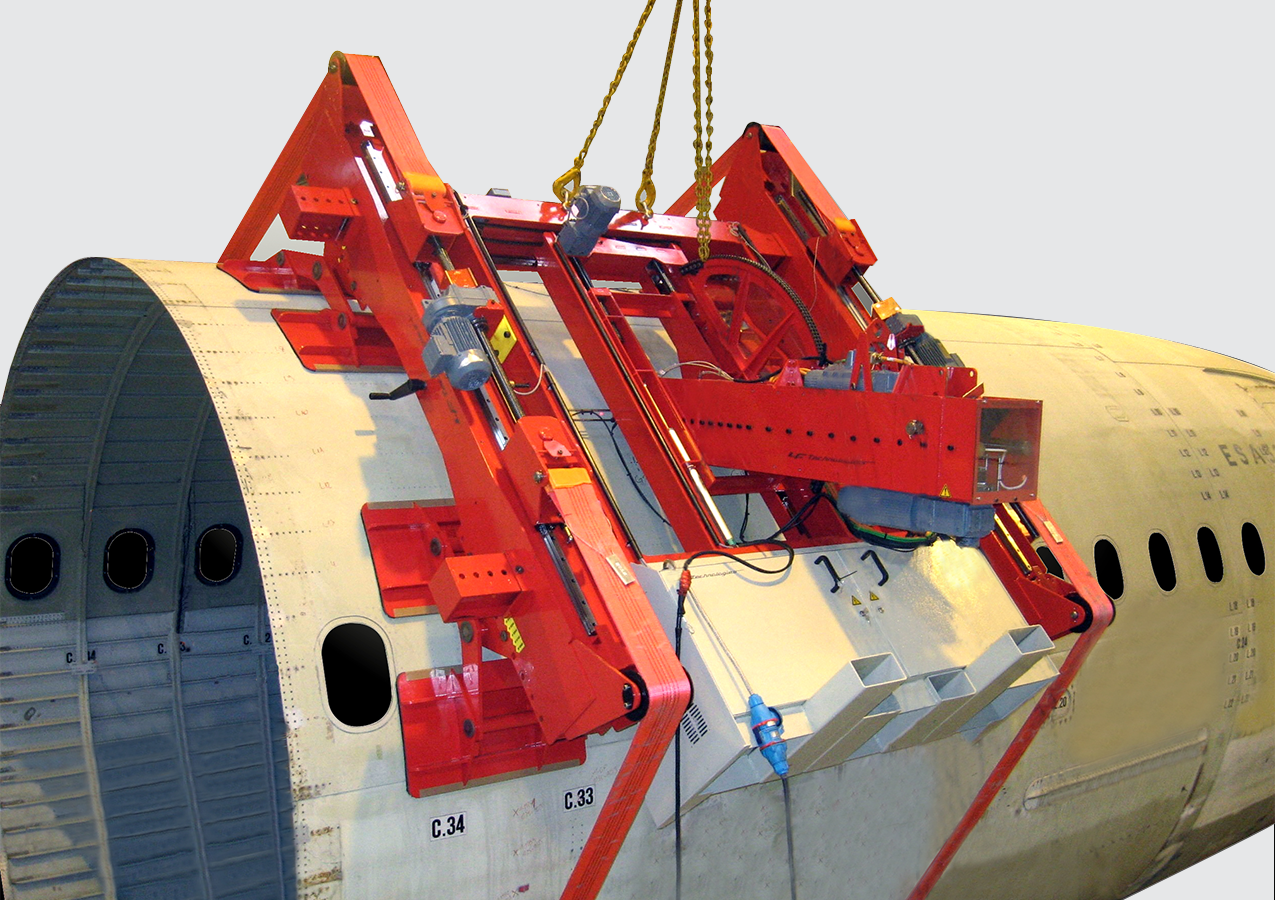
Combined static / dynamic impactor
The combined static/dynamic impactor is used to simulate impacts to aircraft cabins. A laser pointing and distance measuring system makes testing easy and gives accurate results.
THE SOLUTION PROVIDED BY LF TECHNOLOGIES
Main functions
Objective
Carry out impact tests on the fuselage of a “test” aircraft, at an angle of + – 50° to the horizontal. The test machine must perform quasi-static impact tests with adjustable force and dynamic impact tests with adjustable speed and energy, and without rebound.
The tests carried out initially serve to reproduce the deformations observed in reality, in order to estimate the criteria of force, energy and impact speed that generate this type of defect.
In a second phase, the equipment is used to qualify materials or carlingues, by applying impacts that simulate real conditions of use.
Problematic issues
The first challenge is to be able to carry out these tests anywhere in the aircraft’s fuselage, with thrust forces of up to 80kN.
The second problem concerns dynamic tests, which require a purely inertial and passive impact, i.e. generated by the speed of a moving mass, with no active support from the system.
Solution and result
Our experts have designed a machine capable of performing dynamic impact and quasi-static indentation tests. The point of impact can be adjusted within a window of 800 mm horizontally and 400 mm vertically.
A spherical impactor guided by a carriage makes the impacts. The impact energy of the dynamic tests is adjustable and ranges from 50 to 500 Joules. An electric cylinder pushes the impactor to perform static tests up to 80kN.
During dynamic tests, the mass is propelled by an electric servomotor, then released just before impact to ensure a passive, inertial shock. As soon as the impact is detected by the system, the servomotor hangs up the impactor to avoid any rebound.
The test bench is fitted with a mechanically welded steel support to match the shape of the fuselage during testing. It is secured by wide straps placed around the cabin, and the tightness of these straps is measured and checked.
Laser pointing and relative distance measurement options are available to facilitate accurate impact positioning and measurements.
The static dynamic impactor can be adapted to different fuselage diameters (4 to 6 m) using adjustable skids.
Measurements are taken automatically by PC using special software designed exclusively for this machine. A remote control is available to control strap tightening and impactor orientation without the need for a PC.
The impactor has a floating housing equipped with an emergency stop to ensure operator safety.
Products testedA control PC, using software developed under LabVIEW, performs the control and measurement functions.

Aircraft cabin
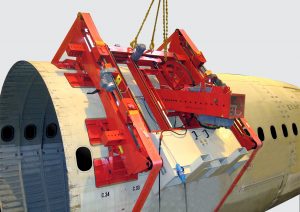
Combined static-dynamic impactor
The dynamic test bench enables impact tests to be carried out in any orientation (horizontal or vertical).
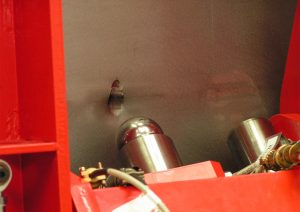
Impact test on aluminium sheeting
Essai d’impact sur tôle d’alu
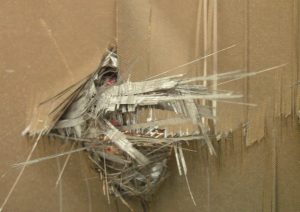
Composite impact test
Composite impact test
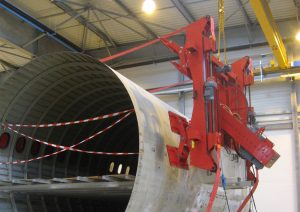
Machine installation on the cabin
Installation of the jet engine on an aircraft fuselage
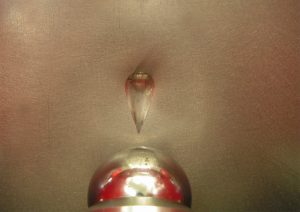
Impact mark
Impact mark made between 50 and 500 joules
Aircraft cabin impact test
The tests carried out are used to reproduce deformations, in order to estimate the force, energy and impact velocity criteria that generate this type of defect.
OUR KEY TEST BENCH FOR THESE TESTS Combined Static Dynamic Impactor
MCI
Main functions
The combined static/dynamic impactor allows to carry out impact tests in all orientations (horizontal or vertical). The shocks are generated by a linear impactor, driven by an electric servomotor. The position and speed measurement with respect to the impacted object makes it possible to measure the potential energy of the shock and the energy absorbed by the sample.
The position and orientation of the impact are adjustable and motorized.
This bench also enables to conduct static compression tests up to 80 kN.
Operating mode
The machine is attached to a test support or directly to the tested element. This hooking is achieved by an automatic servo-controlled system of tightening straps which allows to avoid the use of a gantry of large dimensions (test on an aircraft for example).
The user regulates the position and orientation of the impactor. The test bench automatically searches for a contact position. The impactor is then powered onto the product/sample at a regulated speed. The impactor is automatically caught up to avoid shocks after rebound.
The differential position of the impactor/target is measured by a laser measuring.
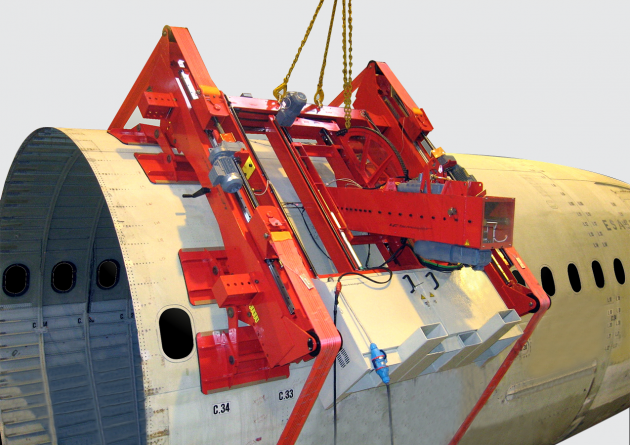
Bench developed to meet these standards:
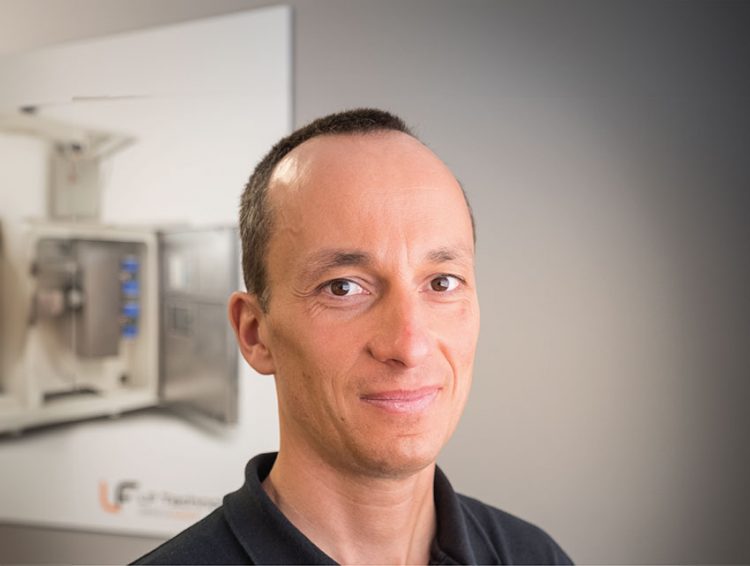
Do you have a project in mind ?
I'm here to advise you and propose solutions tailored to your needs.
Benoit Pelloquin
Mechanical Division
Other sector applications
Discover other test benches and special machines designed and built by LF Technologies.