What methods are used to test pipes in the building industry?
Pipe testing is frequently used in the construction industry. Whether it’s to check the condition of a pipe, verify that a hose or other equipment is working properly. They are essential for user safety and help detect any problems such as leaks, damage or potential obstructions. Tests are also used to check the quality of circulating water and air. An overview of the different pipe testing methods available.
SOMMAIRE
There are a number of different pipe testing methods for the building industry, depending on the characteristics and requirements of the installation. Here are some examples of tests that can be carried out on pipes:
- Pressure test: The purpose of this test is to subject the pipes to a pressure higher than that which will be exerted during normal use. The aim is to check that they don’t leak and that they can withstand pressure.
- Flow test: This test involves circulating a fluid through the pipes. This is usually done using water, with flow and velocity measured at various points in the system. The aim is to check that the pipes have sufficient cross-sectional area to handle the required flow.
- Leak test: The principle of this test is to use a leak detection method. In the same way as acoustic listening or gas detection, we try to find any leaks in the pipes.
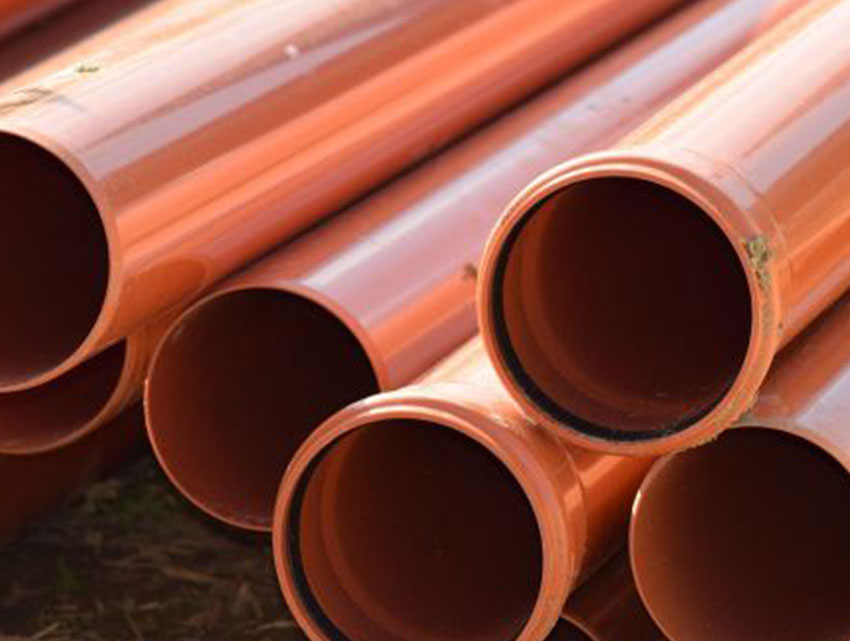
In addition to the tests mentioned above. (pressure test, flow test, leak test and resistance test), here are some other examples of tests that can be performed:
- Leak test : A leak detection method is used for this test. The principle is the same as for the leak test. We use the inert gas or water injection detection method to check that the pipes are leak-free and watertight.
- Flexibility test: This test subjects pipes to bending forces. It is carried out because it is important to know whether the pipes are flexible enough to withstand the movements of the installation without breaking or deforming.
- Durability test: The aim of this test is to subject the pipes to temperature, pressure and chemical conditions similar to those to which they will be subjected during normal use. This ensures that they can withstand wear and corrosion over the long term.
- Safety test: This test checks that the pipes comply with safety standards and regulations. More specifically, in everything that concerns the materials used, dimensions, pressures and maximum temperatures.
- Compatibility test: The purpose of the compatibility test is to check that the pipes are compatible with the fluids that will be circulating in the system. Factors such as chemical composition, temperature, pressure and other parameters have to be taken into account.
- Joint condition test: As the name suggests, the purpose of the joint test is to visually inspect pipe joints. During this procedure, any damage such as cracks, leaks or deformations must be identified.
- Testing the condition of pipe supports: The last test on this list is to check that pipe supports are in good condition. They must also be strong enough to hold the pipes in place without the risk of unhooking or deformation.
Do you have a project ? Contact our test bench experts
Discover other articles and tips
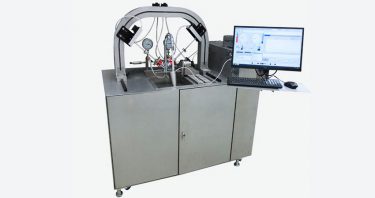
Who are the test benchusers?
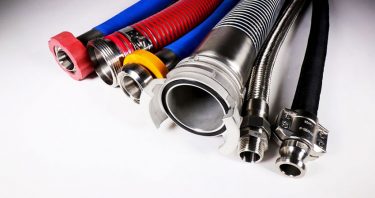
What are the most important tests on sanitary hoses ?
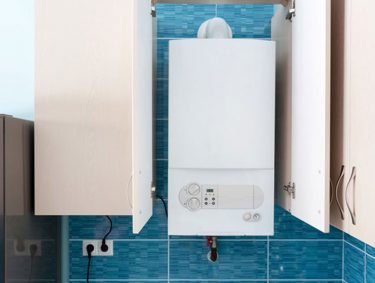
What are the main types of water heaters ?
