BURST PRESSURE TESTING
The concept of burst pressure testing is based on a rigorous experimental procedure aimed at assessing the maximum resistance of a component, a welded assembly, or a hydraulic system under pressure. This method involves applying an increasing internal pressure, measured in bars, to the test product until it reaches its point of rupture or failure. This process not only determines the resilience limits of the materials but also plays a crucial role in preventing potentially hazardous structural failures.
LF Technologies: Precise, safe burst testing
As a specialist in the field of test benches, LF Technologies is committed to providing advanced solutions for pressure testing. Our burst test benches, equipped with servo-motorized plunger piston technologies, offer unrivaled precision in controlling pressure build-up and a fine detection of burst pressure, while ensuring a high level of safety for users.
Our key test bench for burst pressure testing – CRASH-TUBE
This bench is designed for conducting proof pressure and/or burst tests on flexible hoses. It is capable of testing:
- Long corrugated tubes, which deform significantly when pressurized.
- Short smooth tubes, which possess a very high resistance to pressure.
This bench is equipped with a static pressure generator, specially developed by LF Technologies for these testing conditions.
The pressure generator allows for a gradual increase in pressure, as well as pressure holding stages, with controlled pressure (even in the case of creep under pressure of the tested product).
The very gradual and steady pressure increase enables highly precise detection of the maximum burst pressure or the formation of a hernia on the tested tube.
The pressure generator is a motorized syringe. The precision control of this motor allows for fine measurement and regulation of pressure, with a user-configurable pressure rise rate, as well as automatic detection of the rupture point. This technique also ensures intrinsic safety for the user during a burst (as there is virtually no energy storage in the system).
The internal volume of the syringe is sized to cover a wide range of expansion volumes of the tested products. And in case of a greater volume, the machine is equipped with an automatic valve, allowing the pressure in the tube to be maintained while the syringe refills.
The tooling for connecting plastic tubes easily adapts to various diameters and lengths of tubes, without constraining the ends.
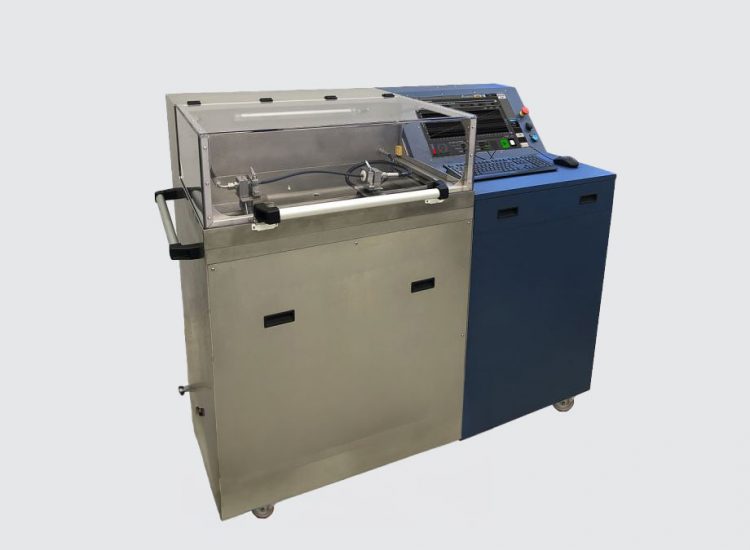
Bench developed to meet these standards:
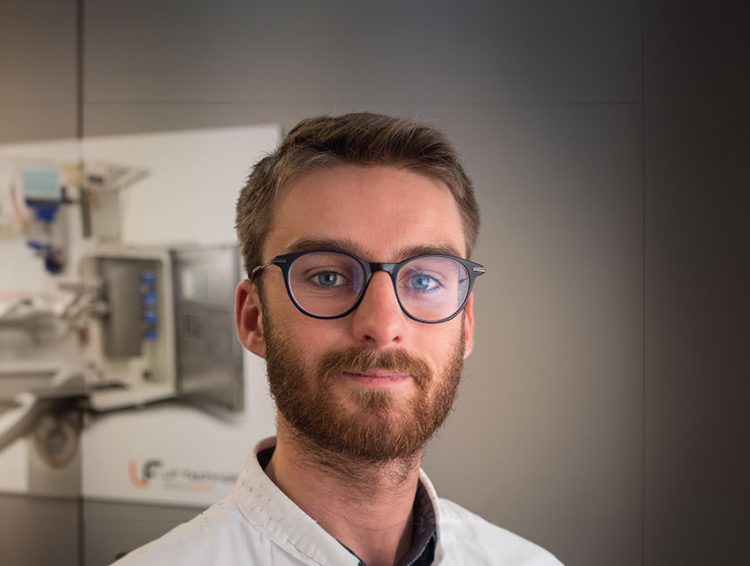
Do you have a project in mind ?
I'm here to advise you and propose solutions tailored to your needs.
Aurélien Cottin
Hydraulics Division
Customer applications
Discover LF Technologies know-how through our customer applications.
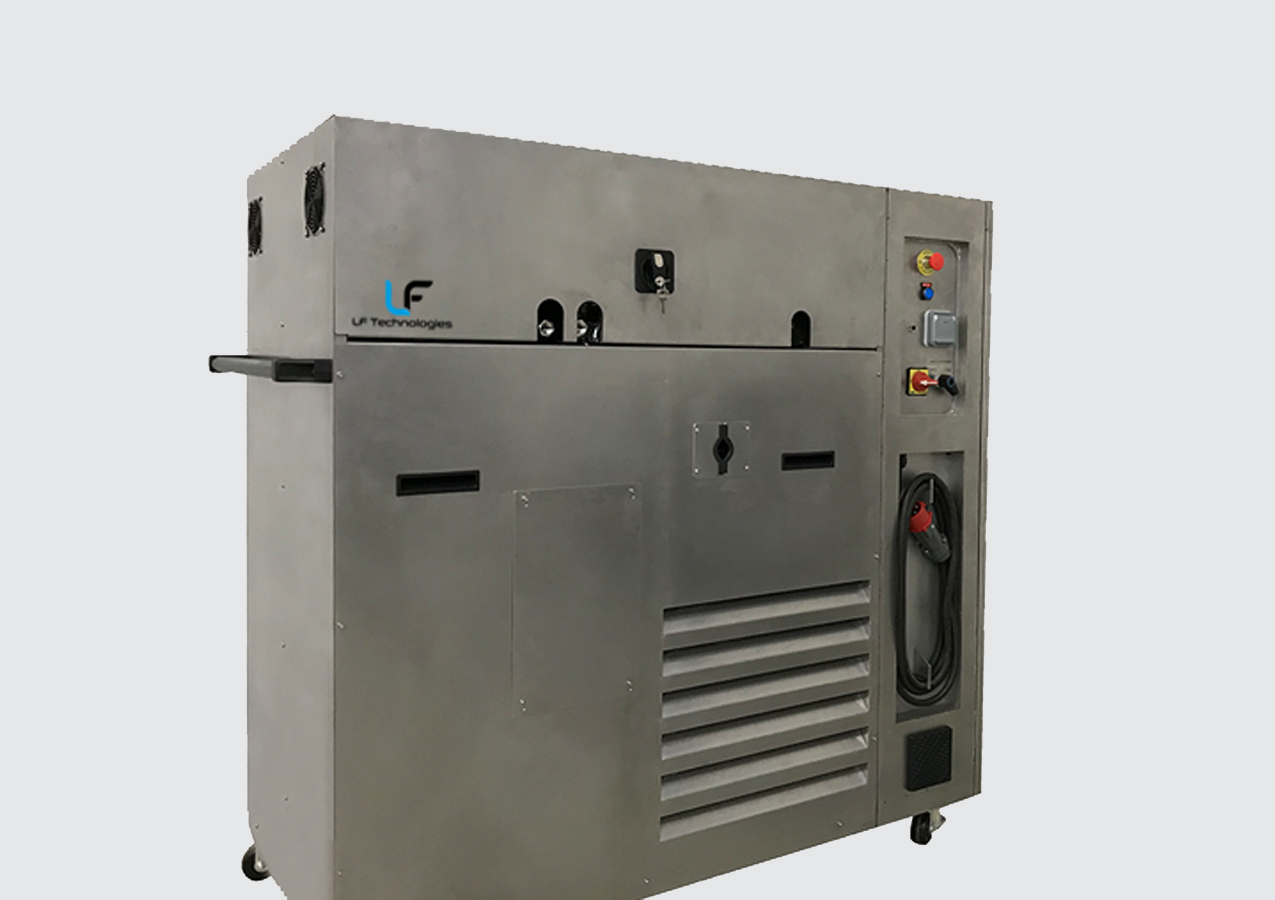
Pressure and temperature control circuit
Special production machine designed to test the resistance of seals to pressure and temperature. This circuit can be connected to a pre-existing hydraulic bench.
They trust us
Principle and Utility of These Burst test
The process of burst pressure testing is meticulous and highly technical. These procedures aim to subject components, welded assemblies, or hydraulic systems to increasing internal pressure, often well beyond their standard operational capacities, until they reach their point of rupture. This reliable technique evaluates maximum resistance and identifies potential failure points of materials and structures.
Importance of Pressure Resilience Tests
These tests are essential for ensuring the safety and reliability of products under extreme conditions. For instance, in the aerospace sector, these pressure resilience tests confirm the ability of components to withstand extreme pressures during flight. In the automotive industry, they assess the resistance of pressurized parts, such as fuel and oil hoses or lines, to prevent operational pressure failures.
Realistic Simulation of Extreme Conditions and Compliance with Standards
The primary advantage of these test procedures is their ability to simulate the real-world conditions that products will face. This enables manufacturers to anticipate how their products will behave under extreme pressures and identify weaknesses before they become critical. These tests are crucial for ensuring the safety of end-users and for compliance with national and international safety standards.
Why Choose LF Technologies’ Hydraulic Test Benches ?
LF Technologies’ commitment to innovation and quality is at the heart of our philosophy. Our hydraulic test benches for burst pressure testing embody this commitment, offering reliable and precise solutions for critical tests across various industrial sectors.
Expert advice
Would you like to find out more about hydraulic test benches? Find out everything you need to know and much more!

What methods are used to test pipes in the building industry?
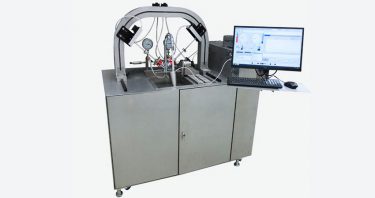
Who are the test bench users ?
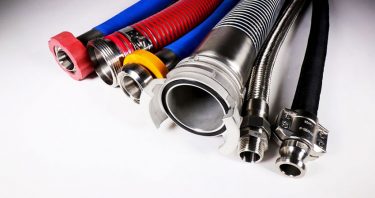
What are the most important tests on sanitary hoses ?
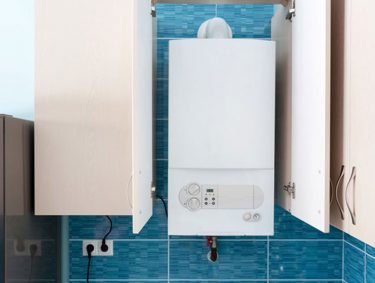